Coupled Electromagnetic-Thermal Model of a Superconducting Motor
The construction of a superconducting aircraft motor demonstrator is underway under ASuMED project. Magnetized stacks of commercial superconducting tapes will be applied in a rotor in place permanent magnets. The rotor will be cooled with liquid hydrogen down to approximately 20K to provide favorable conditions for the superconductors. The stacks in the context of the machine operation exhibit interesting thermal and electromagnetic behavior.
In the motor the magnetized stacks are subjected to time-varying magnetic fields. It causes demagnetization and heat generation. The trapped magnetic field is thus decreased, potentially leading to the deterioration of the obtainable power output. Anistropic heat transfer in the stacks exacerbates the problem. Deep understanding of the stack behavior is crucial to select the proper shape of stacks and build a reliable motor. In order to investigate the intertwined phenomena the numerical model is created.
In this contribution the description of the numerical model of the rotor and the examples of results are presented. Thermal behavior is modeled using the Heat Transfer module, with the consideration of complex structure of superconducting tape included as anisotropic, temperature-dependent thermal conductivity. Magnetic field and electric current in superconducting tapes calculated with Magnetic Field Formulation interface from AC/DC module. The link between between them is electromagnetic heat generation and dependence of critical current density of a superconductor on temperature.
The model predicts the behavior of the stacks depending on geometry of the rotor, applied magnetic field and temperature. The possibilities of the improvement of the operation of the motor, such as the optimization of the shape of the stacks and their composition, are found and analysed. Comparison with experimental data is provided when possible. The results of the numerical analysis will be used in the design and manufacturing the stacks for the motor demonstrator.
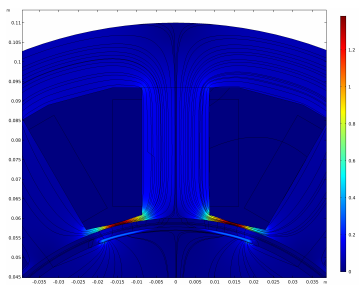